Dec. 04, 2024
Introduction of new models
An appealing interior space
within a compact body
Honda FREED
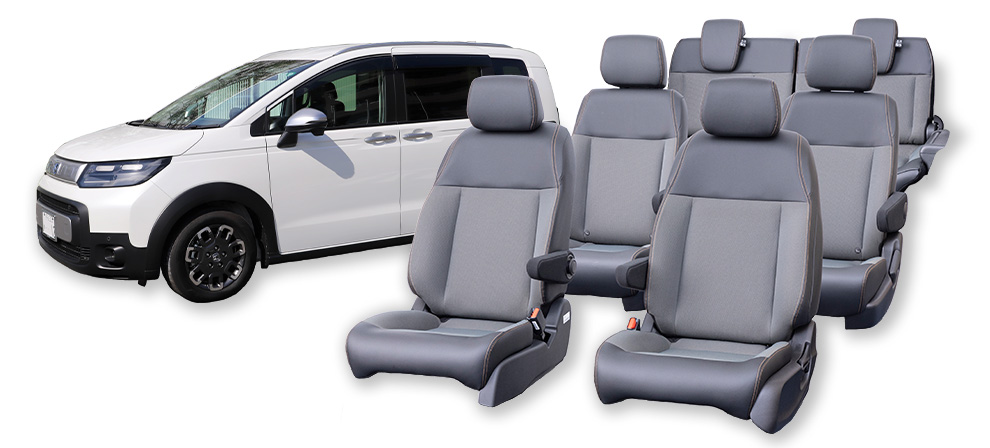
The redesigned FREED launched by Honda Motor Co., Ltd. in June 2024 features seats manufactured by TS TECH.
We spoke with members of the project team about the process of developing the seats for this compact minivan,
which has been delivering smiles to many users since the original model.
Profile
-
Taiki Takeuchi
Design Department 1
Design Project Leader
Joined TS TECH in 2009, and works in the Design Department. After working on developing seats for automobiles, worked in North America from 2013 to 2018. For the new FREED project, served as Design Project Leader for the new FREED.
-
Tsuyoshi Komori
Model Control Department
In charge of design and appearance finishing
Joined TS TECH in 2014, and works in the Model Control Department. Engages in seat appearance finishing and other duties primarily for minivan models. For the new FREED project, sought to produce high-efficiency, high-precision patterns based on appearance and deformation analysis.
-
Hirokazu Natori
Purchasing Department 1
In charge of cost management
Joined TS TECH in 2007, and works in the Purchasing Department. Mainly engages in the procurement of materials such as trim covers and urethane. For the new FREED project, worked with suppliers to help optimize costs.
NatoriThe seats for the previous FREED model were manufactured by another company. So, to win the contract for the new model, we needed to propose solutions that exceeded customer expectations in terms of specifications, manufacturing, and costs. As the customer had especially high expectations for costs, it was vital to enhance competitiveness in this area, when competing against a manufacturer who had the advantage of being able to use parts from the previous model.
Given inflation and rising material costs, the negotiations with our suppliers were pretty challenging. We were able to make headway in the negotiations through close discussions with the suppliers on finding ways to enhance competitiveness while sharing our vision for the future.
How did you respond to customer needs?
TakeuchiWhen considering specifications, we carefully considered how to design the streamlined and appropriate seat frames to achieve the dimensions and appearance demanded by the customer. We then looked at the specifications for the molds required to efficiently manufacture the seat frames while helping to reduce costs. We also used the approach of updating specifications for our previous seats that were well received by customers to suit the new FREED, rather than relying solely on new designs. That helped reduce losses both during the development process and during the mass production process. We drew on existing designs, which made it possible to keep costs low while maintaining competitiveness. This flexible approach improved efficiency throughout processes ranging from development to mass production, contributing significantly to reducing losses in the production process and ultimately leading to winning the order.
KomoriThe front seats use our flagship seat frame, which is designed to distribute body pressure evenly for enhanced comfort. The design features rounded seat edges, making it easier to access the rear seats for improved walk-through accessibility (Fig. 1). We also increased the mid-seat cushion thickness by 20 mm for improved thigh support, allowing passengers to sit with a more natural posture for enhanced comfort (Fig. 2).
TakeuchiWith the rear seats, we also sought to maintain or improve comfort compared to the previous model. We made the seats thinner and lighter to improve ease of use without compromising on the level of comfort. This made it possible to increase the space available for cargo compared to the previous model. We also redesigned the seat flip-up mechanism, lowering the pivot point to make it easier to use for smaller users (Fig. 3). The FREED allows multiple seat configurations to suit user needs based on their lifestyle, from three-row layouts to cargo-focused two-row layouts (Fig. 4).
KomoriI think the success of this project was due to the clear guidance provided by the new FREED Large Project Leader and the cooperation provided by the development members and the production and purchasing departments. Even when facing technical challenges during the development phase, the whole project team actively worked together, rather than passing on responsibilities to other departments.
NatoriThose of us in the Purchasing Department worked closely with both our suppliers and the development and production departments, with a focus on cost management. This made it possible to meet customer expectations and achieve even better results. I believe that the way everyone worked together to ensure the success of the project enabled us to create the high-quality seats.
TakeuchiThere was a lot of trial and error involved in bringing this product to reality, but we were able to move forward as a unified team, without drawing lines between the departments. The success of this project is truly the result of the efforts of all the members involved. As the Design Project Leader, I hope those who gained experience through this development project will become leaders of the next generation of development projects. To ensure the TS TECH Group remains “a company sincerely appreciated by all,” we are committed to passing on the spirit of manufacturing to future talent and to pursuing new value as a team.