Value Chain (Value Creation Strategy)
The TS TECH Group achieves value creation through manufacturing that yields high-quality products and services.
We aim to maximize corporate value by leveraging mutual cooperation and synergies among the functions of each value chain. In this effort, we make optimum use of all the management resources we have developed over our 60 years in business with the support of our stakeholders.
Value chain
- R&D
- Creating innovative, attractive products and technologies
- Sales
- Proposing competitive products to satisfy customers' demands
- Purchasing
- Offering stable provision of components by maintaining a strong supply chain
- Manufacturing
- Operating highly efficient mass production systems in 13 countries
- Quality
- Using a quality control system to ensure stable supply of safe and secure products
Feedback
- Titles shown were current as of the publication of the “TS TECH Integrated Report 2023” (Sept. 2023).
Research and Development
The transformation of mobility brought about by recent technological innovations is completely changing the value that has been demanded of automotive interior products in the past. We are leveraging this change as an opportunity to drive our Group’s further business growth. We are focusing on creating new value not only in the seats but also throughout the entire vehicle interior space. In order to achieve sustainable growth together with society, we will conduct research and development from various perspectives, including technological evolution from both the development and manufacturing axes, with the aim of quickly commercializing environmental technologies that are ahead of other companies.
Companies cannot create value simply by accumulating conventional technologies. Based on our corporate philosophy of being “A company dedicated to realizing people's potential,” we strive to foster product developers, innovate with the diverse ideas they generate, and create unique technologies that have never existed before.
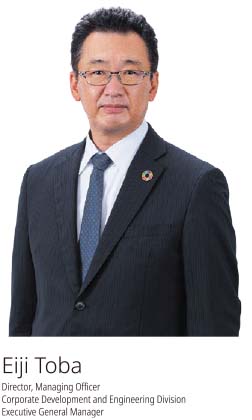
Basic Policies on Value Creation
- Creating and delivering appealing products and technologies
- Enhancing our system and software development capabilities beyond the framework normally required for a parts manufacturer
- Developing environmentally friendly products and manufacturing technologies that help build a sustainable world
- Ensure reliable quality assurance from the outset of development
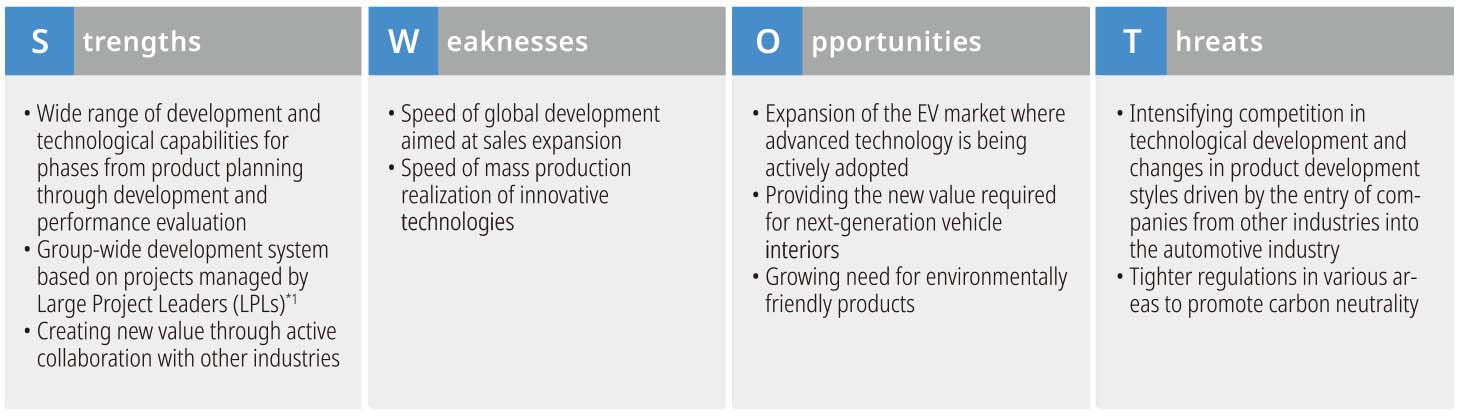
Securing cabin coordination capacity
The Group is working to secure cabin coordination capacity to create the new functions and technologies that will be required in the next-generation vehicle market, characterized by advanced autonomous driving technology and widespread transition to EVs. This will enable us to propose products for the entire vehicle cabin, and go beyond our conventional business areas of seats and doors. We aspire to propose the entire vehicle interior space as an appealing product. Toward this end, we are accelerating basic research related to the needs of people as the riders of next-generation vehicles. We are also promoting R&D aimed at establishing completely new functions and technologies created through collaboration with other industries. Moreover, by working on the development of highly efficient mass production technology that can easily be adapted to new construction and materials, we are building a production system that will allow us to deliver the technologies we develop as competitively priced products.
Ongoing pursuit of environmentally friendly technologies
In order to help reduce the environmental impact of automobiles and help build a more sustainable world, we are working to build EV-compatible technologies that help reduce the weight of vehicles, as well as those that allow non-sustainable materials to be replaced by sustainable ones,*2 such as recycled and biomass materials. To address issues such as a decline in seat cushioning performance caused by sustainable material adoption, we are reexamining vehicle seat construction based on the unique expertise that the Group has accumulated over the years. This approach will enable us to deliver both environmental performance and comfort. The Group is also proposing seats constructed with a low hip point, which helps in the creation of streamlined designs for EVs with lower air resistance and improved power usage efficiency. Our aim is to keep growing along with society by creating new environmental technologies that automakers cannot achieve on their own.
- A development system that assigns LPLs to coordinate all departments, including overseas bases, and provides total management from planning to mass production
- Raw materials that are derived from continuously available resources and have a low environmental impact throughout their life cycle
Sales (Honda Group)
Approximately 90% of the TS TECH Group’s consolidated revenue comes from sales to the Honda Group, consisting of Honda Motor Co., Ltd. and its affiliates. While acquiring new customers remains an important part of our plans for further business growth, the business relationship with Honda will continue to be an important foundation of TS TECH’s operations, forming the backbone of the Group.
Currently, our products account for approximately 60% of the seats installed in vehicles sold by Honda. Our goal is to increase this share to 70% by 2030. We aim to further increase our market share with Honda not only by developing products that meet the needs of end users but also by providing a variety of proposals that meet the specific needs of Honda.
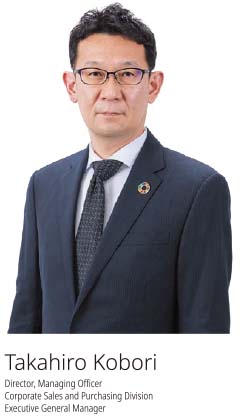
Basic Policies on Value Creation
- Offer appealing products that exceed customer expectations at competitive prices
- Permanently secure customers’ unwavering trust
- Proposing new vehicle interior value to customers using internal collaboration including regional and functional corporate divisions
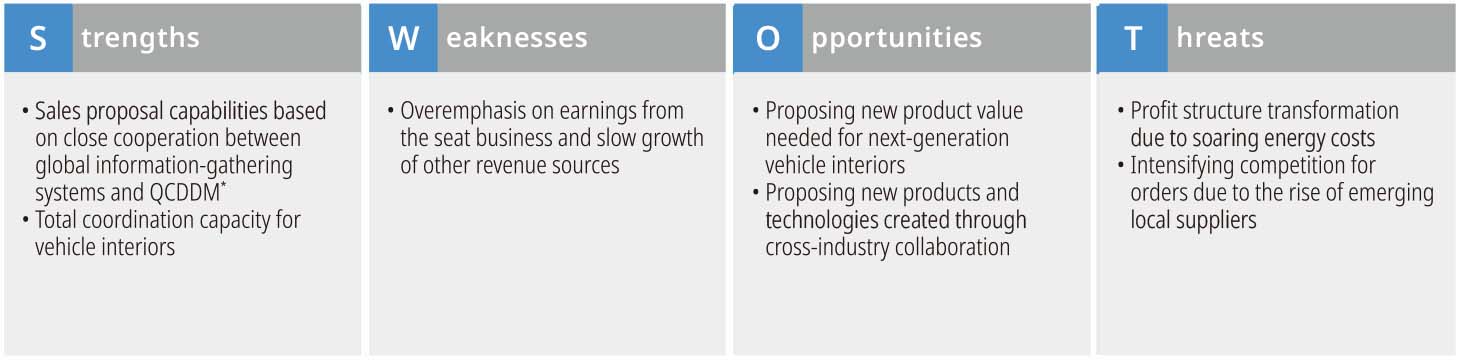
Business development that leverages our strengths
n order to further increase our market share in Honda, in addition to acquiring new commercial rights, we need to ensure that we continue to receive orders for commercial rights for models for which we have already received orders, even after model changes. We will achieve this by creating value that is unique to TS TECH. We do this by further enhancing customer satisfaction through the creation of products that exceed expectations and by co-creating products with the Honda Group from the early stages of development to propose seat products that combine functionality and design in line with customer needs in an unprecedented way.
Moreover, through close cooperation between relevant internal divisions under our Corporate Sales and Purchasing Division, which oversees the Honda-related business, the Group is able to offer high-quality, competitive products in any global region. We aim to acquire further commercial rights by taking full advantage of the geographical advantages provided by our overseas sites, which span 13 countries worldwide.
Expansion of parts orders, leading to vehicle seat commercial rights
A vehicle seat is made up of various parts, such as the seat frame and trim cover. The Group has acquired commercial rights not only for the seat itself but also for these parts, and is developing products tailored to each vehicle model. Among the seat components, the frame is closely related to the seat itself, and is an important factor in obtaining orders for a particular seat to be developed later. By quickly and accurately identifying customer needs, and by promoting internal collaboration including the Corporate Development and Engineering Division, the Group is working to create a standard seat frame that can be installed in a wide range of vehicle models. By proposing a competitive standard seat frame, we will expand seat frame orders, leading to future orders related to seat commercial rights.
- QCDDM: Quality, Cost, Delivery, Development, and Management
Sales (New Businesses)
In order for the TS TECH Group to achieve further business growth, we will expand sales not only to the Honda Group but also in new business areas beyond that customer, by acquiring new clients and expanding commercial rights. We have long regarded this as an important issue and have undertaken a variety of relevant initiatives, which are steadily delivering results. We are seeing clear signs of future sales expansion, including more commercial rights with Suzuki Motor Corporation and Volkswagen AG, as well as orders from multiple new customers.
The Group’s target for 2030 is that 30% of revenue would come from new businesses. This figure is 7.8% as of March 2023. To achieve the goal, we will leverage the leadership of the New Business Management Division to carry out strategic sales activities that reach customers worldwide.
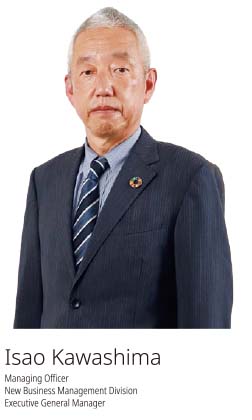
Basic Policies on Value Creation
- Obtaining commercial rights orders with high added value using planning proposals that anticipate customer needs
- Proposing products based on existing commercial rights (expanding adoption to derivative models)
- Pursuing strategic sales development focusing on target commercial rights to increase the likelihood of securing orders
- Strengthening the competitiveness of our European sites to promote commercial rights expansion
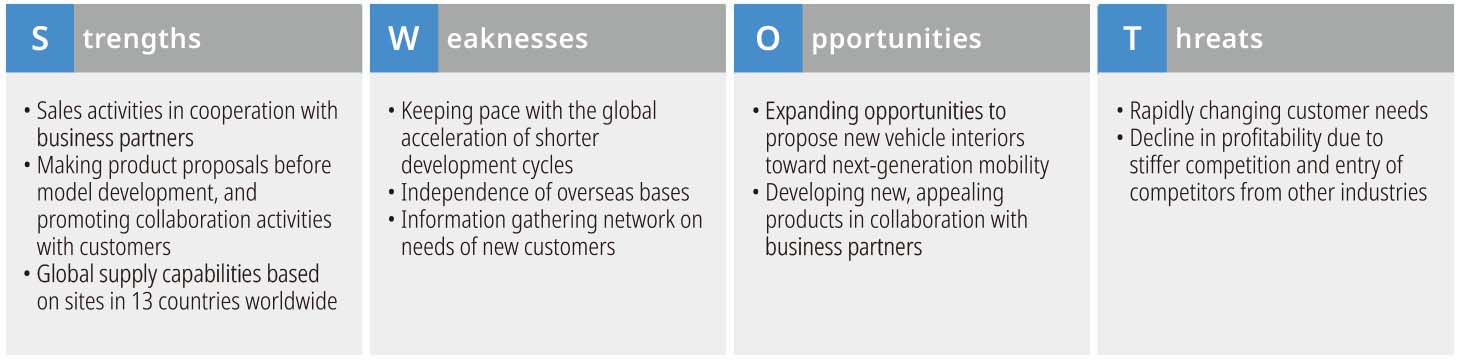
Ongoing new business expansion
We will gain the trust of customers worldwide and acquire new commercial rights by carrying out highly strategic sales activities that make the most of the Group’s resources. We will quickly expand orders by implementing optimal sales approaches utilizing our Group’s geographically advantageous bases according to the customer’s location, and by making technical proposals for specific target vehicle models, including horizontal deployment to derivative models of technologies that have been highly rated under existing commercial rights. In addition, through collaboration between the Corporate Sales Division and the Corporate Development and Engineering Division, we will identify latent customer needs, regularly hold presentations on the functions and technologies required of next-generation vehicle interiors, and participate in customers’ advanced development that will set the direction for future mass-produced models, thereby ensuring the acquisition of commercial rights.
Strengthening the competitiveness of the Group’s new European operations
With sites in Germany and Poland, the TS TECH Group is focusing on further expanding its transactions with European automakers, such as the Volkswagen Group. Thanks to its location, our new vehicle seat production company in Poland, which will begin full-scale operations in fiscal 2024, will be able to supply products at competitive prices to European automakers located in Germany, the Czech Republic, Slovakia, and other countries. Using this as a key site to actively implement sales development in Europe, we will not only expand commercial rights with existing customers but also build relationships with new ones. Not only expanding production capacity, we will also optimize our production system, including the supply chain, to further grow our business and improve profitability.
Purchasing
The TS TECH Group works hard to ensure that its business activities help to address social issues, fulfilling its policy of realizing ESG management. We are helping to build a sustainable world by promoting sustainability initiatives not only internally but across our entire supply chain.
The Group is striving to advance its core procurement functions by practicing supply chain management to enhance price competitiveness and improving its business continuity capabilities to ensure stable product supply even during emergencies. In addition to this, we are further strengthening our sustainability initiatives by addressing issues such as climate change and human rights. We are working to share our objectives not only with our business partners in Japan, but with all partners worldwide, in order to forge a strong, sustainable global supply chain.
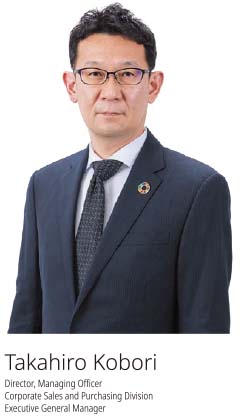
Basic Policies on Value Creation
- Building a supply chain that outperforms those of other companies
- Building a supply chain that supports new business expansion
- Streamlining and rationalizing procurement routes
- Improving QCD* capabilities by enhancing supply chain management
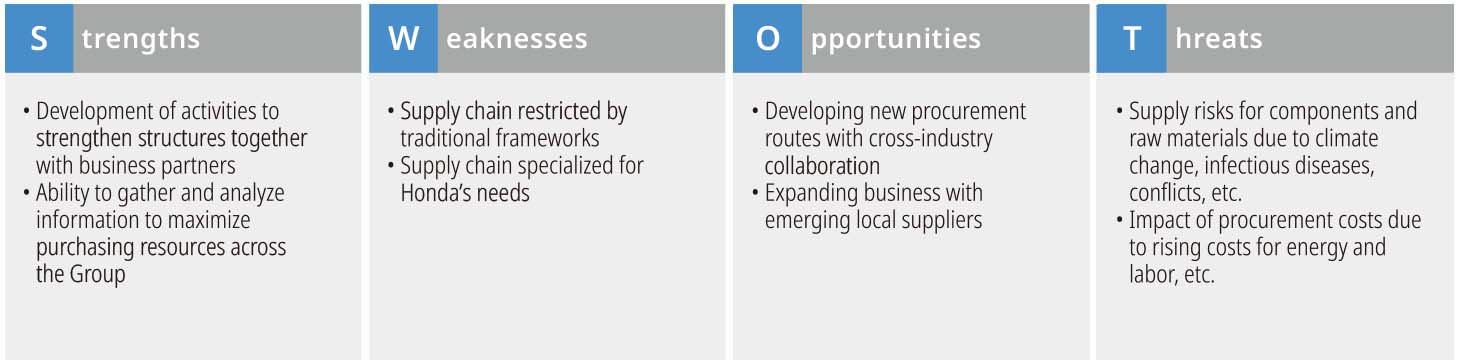
Ensuring the supply chain boosts competitiveness
The technological transformation of mobility is expected to lead to intensified competition among suppliers, including new entrants from other industries. To survive in this environment, the TS TECH Group is working on various measures to increase its competitiveness in the area of purchasing as well. In addition to further enhancing collaboration with business partners, we are completely updating the supply chain we have built over the years. Our aim is to boost competitiveness by increasing the Group's profitability based on a thorough streamlining of procurement routes and an expansion of procurement of parts at sites outside Japan. Moreover, we will establish procurement routes to accommodate the expansion of sales to non-Honda customers and to ensure a stable supply of increasingly diverse and multifunctional products. In this way, we will strive to optimize the supply chain from various perspectives and seek to maximize added value across the Group.
Building a sustainable supply chain
The TS TECH Group works together with business partners to mitigate various risks and build a sustainable supply chain that complies with relevant laws and social norms. Using the TS TECH Supplier Sustainability Guidelines, we ask our business partners worldwide to understand and adopt sustainable practices. In the environmental field, our aim is to achieve carbon neutrality across the supply chain. We are working to improve calculation accuracy for Scope 3 emissions and encourage business partners to further reduce their CO2 emissions by improving communication with them. The Group updates its supplier guidelines as necessary, while striving to remain a company sincerely appreciated by all across its supply chain.
- Quality, Cost, and Delivery
Manufacturing
Manufacturing is the core activity of the TS TECH Group, so one key to achieving further growth will be to improve our manufacturing capabilities. We must do this in a way that will allow us to effectively respond to an increasingly uncertain business environment, along with changes in raw material and product construction requirements resulting from industry trends such as CASE and MaaS. By building a highly efficient manufacturing system that outperforms those of other companies, for instance by adopting more automation and digital technology, we aim to forge a corporate structure that can respond to any sudden changes that can affect production, such as semiconductor supply shortages.
Meanwhile, we are working to establish new technologies that will undergird the creation and mass production of unprecedented products. To do this, we will develop environmental technologies that prevent or reduce environmental impact, as well as next-generation technologies suitable for EVs and autonomous vehicles. The Group’s development and manufacturing areas will work together to create these technologies, thereby promoting further business growth and helping to build a sustainable world.
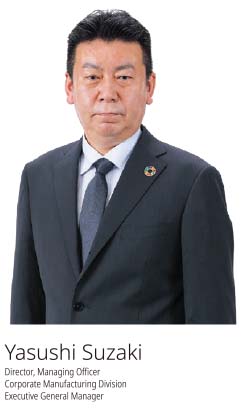
Basic Policies on Value Creation
- Improving our manufacturing for higher efficiency and sustainability
- Providing innovative production technology to Group companies and strengthening control functions
- Building highly efficient production lines using automation and more advanced equipment and molds
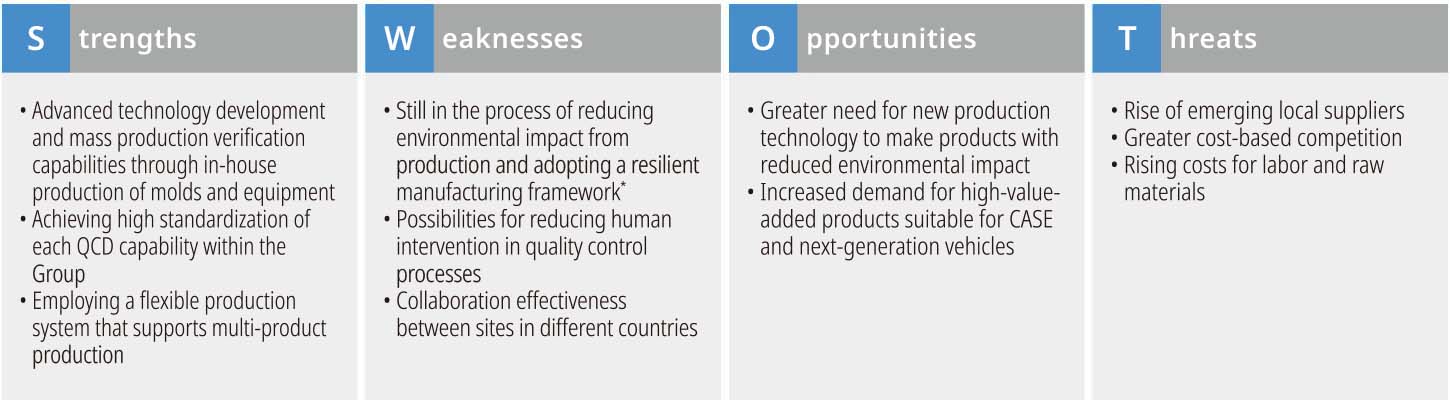
Ongoing advancement of TS TECH manufacturing
The TS TECH Group is optimizing its manufacturing system to better respond to the diversifying needs of customers, while delivering a stable supply of high-quality competitively priced products to the world. In addition to thorough efficiency improvements using digital transformation, IoT, and other advanced technologies, we are also promoting further quality improvements, such as strengthening assurance of defect-free processes using a quality determination system based on AI analysis. Due to the nature of vehicle seats, which are made up of numerous components with different properties, many processes still need to be completed by hand. It is therefore important not only to adopt more automation but also to provide a good working environment for every employee involved in manufacturing. Accordingly, we will strive to promote employee diversity on production lines. This includes strengthening our ability to develop in-house equipment to reduce workloads, an effort that will be driven by employees with a deep understanding of the front lines.
Sustainable production system
The Group’s long-term environmental goal is to achieve carbon neutrality in its business activities, and it is working to reduce its environmental impact by taking measures such as conserving energy. While advancing technologies to increase production efficiency, we are planning to further improve the efficiency of our production equipment by, for example replacing outdated equipment and installing inverters. Additionally, we intend to reduce CO2 emissions and energy costs from various angles. This includes horizontal deployment of energy conservation diagnoses by facility experts from Japan to other sites around the world. We will also build a production system that is sustainable from a variety of perspectives by, for instance, developing equipment that uses regenerative energy and devising karakuri mechanical ways to automate work without using electricity.
- Framework to create a financial structure that generates a certain amount of profit even when earnings drop
Quality
The TS TECH Group’s products are essential vehicle components that help protect human life. This is why we believe that quality is the most important reason that automakers choose TS TECH. It forms the basis of their trust in us as a manufacturer. The mission of the Corporate Quality Assurance Division is to consider all the measures that need to be taken to ensure that the Group never produces or ships defective products. Its mission also includes overseeing the implementation of quality assurance measures, and ensuring that everyone in the Group fully understands the importance of quality. We work not only within the Group but also in cooperation with business partners who supply our parts and raw materials.
By promoting the universal awareness that every individual is responsible for quality, and linking this mindset to quality improvements, we are building a quality control and assurance system that will ensure TS TECH continues to be the choice of customers—an objective the Group cannot achieve without partner cooperation.
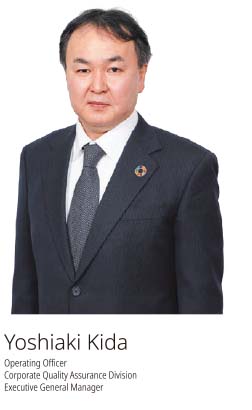
Basic Policies on Value Creation
- Provision of safety and security to customers
- Stable provision of products with the same high level of quality worldwide
- Earn top quality rating from customers all around the world and establish TS-Quality brand
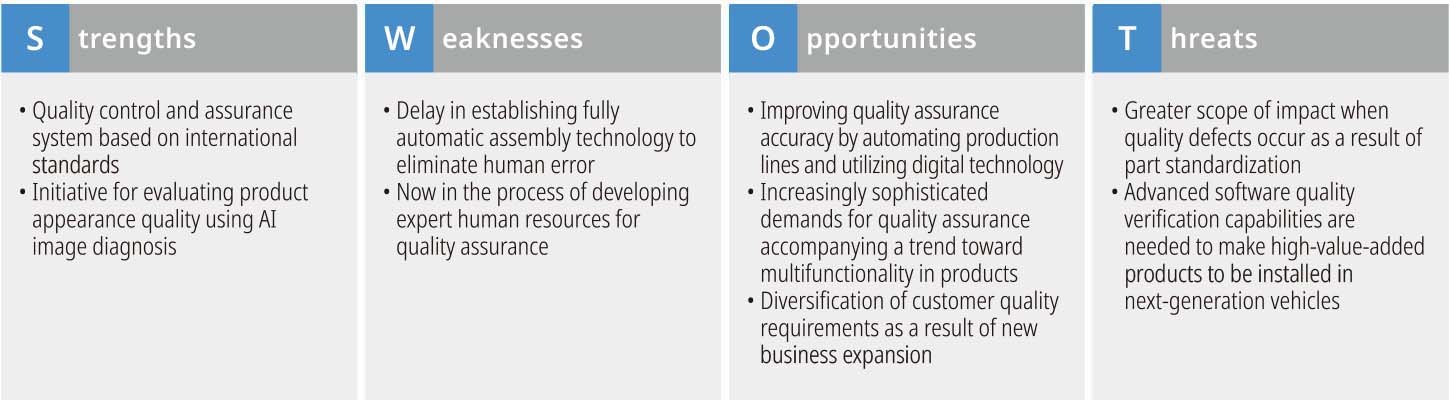
Ensuring quality assurance through defect source management
The Group implements defect prevention in all processes of its value chain, from product planning, design, development, and manufacturing, to procurement, equipment maintenance, and maintenance of quality control systems. By implementing upstream management that requires investigation of issue root causes and then conducting a series of fundamental process improvements, we have built a reliable quality assurance and management system. This system has led to the creation of product specifications that prevent defects and the automation of production and inspection processes that make quality assurance more effective. We also conduct Group-wide continuous quality assurance training and TC Circle activities (improvement activities undertaken by small groups) in order to keep increasing each employee’s knowledge and awareness of quality control and business improvement, and strive to improve product quality in each process.
Enhancing quality management
In April 2023, the Group established a new quality control department with the aim of enhancing quality management. This department will take the lead in improving the Group's quality auditing function by conducting physical inspections at each site, and by thoroughly monitoring and managing operations to ensure that quality assurance is being carried out using the proper processes. The department will also prepare important management points for quality assurance and communicate them throughout the Group. By carrying out quality control in line with these key points at all sites, we will build a system that ensures early resolution of quality issues and keeps the product supply system healthy. By building a quality assurance and management system that enhances corporate value, leveraging close cooperation between the Corporate Quality Assurance Division and Group sites worldwide, TS TECH will continue to be “A company sincerely appreciated by all” for delivering safe and reliable products.
Important Departments That Support the Group’s Value Chain
Fully utilizing IT to maximize the Group’s performance
The IT Department collaborates with Group sites and departments worldwide to investigate optimal system specifications. We are working on updating old systems that hinder digital transformation efforts, automating operations, and digitizing business processes including performing electronic approvals. Additionally, as part of work-style reform, we are building a remote work environment, while maximizing the performance of the entire Group in terms of both online applications and infrastructure.
In recent years, information leaks and suspension of business operations due to cyberattacks and system failures have become significant risks for companies. Addressing this, we are providing IT security training for employees using email, eliminating vulnerabilities in internal systems, and conducting external monitoring to detect unauthorized system access and suspicious online behavior. By working to strengthen information security Group-wide through activities such as these, we are protecting our intellectual capital and building a solid business foundation that can maintain the trust of our stakeholders.
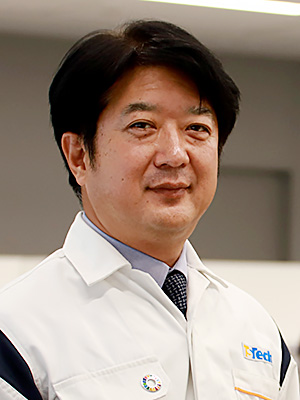
Corporate Administration Division
IT Department
General Manager
Yoshihisa Masubuchi
Trade management to promote a competitive supply system
We promote the local procurement of parts and materials at sites outside Japan as a priority strategy of the 15th Medium-Term Management Plan. At the same time, we also work to stabilize and improve the efficiency of supply and procurement activities that involve international trade.
In order to facilitate trade procedures and provide the flexibility to respond to changes in the international situation, we have established a system for handling customs procedures internally. By meeting the trade security standards set by the Japanese government, we have obtained Authorized Economic Operator status for customs procedures in Japan. This allows for more efficient customs clearance, including the omission of cargo inspections. In the event of any maritime transport delays, we can quickly obtain export permits for alternative shipping options. These capabilities give the Group’s worldwide production network superior reliability and flexibility.
Moreover, when utilizing the Group’s trade network, we take into account the complex economic partnership agreements that exist between countries. By making full use of this knowledge, we are reducing customs costs and helping supply Group products at competitive prices.
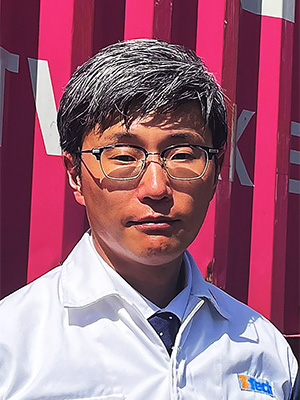
Corporate Manufacturing Division Manufacturing Planning Department Foreign Trade Management Section Manager
Ryuto Kusumoto
Developing intellectual property strategies using both proactive and protective approaches
One of the important ways for the Group to maintain its long-term competitive advantage is to protect and utilize the results of its R&D operations, which become intellectual property (IP). When it comes to its proprietary technologies that can help build a sustainable world and innovative technologies, the Group works to maximize the value of this intellectual property by implementing a variety of proactive initiatives to build a strong patent network. We also implement protective measures to develop products while minimizing the risk of IP disputes by strategically utilizing patent searches and respecting the intellectual property rights of others, for instance. Our performance on these initiatives has also been recognized by external stakeholders. The Group has been ranked first among all similar suppliers in both Japan and the United States in a third-party survey of the comprehensive patent strength for an entire vehicle seat lineup.* We will continue to support the Group’s manufacturing with these proactive and protective intellectual property initiatives, while ensuring that we leverage R&D outcomes to improve corporate value.
Corporate Development and Engineering Division Intellectual Property Department General Manager
Akira Miyoshi