May 27, 2024
Introduction of new models
Rear seats designed and created through
the joint development of new value
in aspects transcending seating
SUZUKI SPACIA
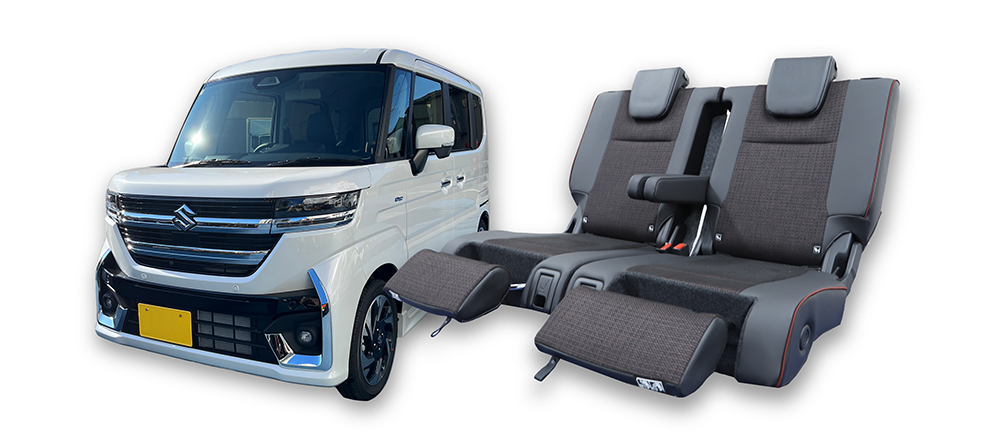
Introduced in November 2023, Suzuki Motor Corporation’s
new Spacia and Spacia Custom models feature rear seats made by TS TECH.
We spoke with members of the project team who developed these seats,
which were created through the unrelenting pursuit of comfort and convenience in order to meet
the diverse needs of end users.
Profile
-
Masaaki Matsushima
Large Project Leader
Joined TS TECH in 1986. Following his assignment to the design department in the Hamamatsu area, he worked as a design staff member at various facilities on seats for motorcycles and automobiles. As a Large Project Leader, he has led various projects covering a wide range of models since the mid-2010s.
-
Shinya Aita
Design Department 2
Design Project Leader
Joined TS TECH in 2009. For most of his career since then, he has worked on designing seats for Suzuki while also working on seat analytics and in other areas for several years. He served as Design Project Leader on this project.
-
Takeshi Sakurai
Business Development Department
Sales Project Leader
Joined TS TECH in 2003. He has served as a sales contact point exclusively for Suzuki since 2006. He supported development activities with Suzuki in the project, working from a brand new approach based on designing an even better product.
-
Toshihiko Takahashi
Development and Testing Department
Product Performance Verification
Joined TS TECH in 2011. For his first five years after joining the Company, he worked in market research and other activities in the New Product Development Department. He was transferred in 2016 to the Development and Testing Department. On this particular project, he oversaw product performance verification in seat comfort, ease of use, and other aspects.
Could you tell us about the background to the project?
MatsushimaTS TECH has a long history of transactions with Suzuki. Various Suzuki cars and motorcycles have featured seats made at the Hamamatsu Plant. But in the mid-2010s, we lost a contract for passenger vehicle seats produced at the Hamamatsu Plant. This was due to the failure to make progress on competitive advantages. The goal of this development project for seats for the new Spacia was to revive the Hamamatsu Plant, where the atmosphere had grown gloomy due to the sharp decline in production volume.
I worked in the Design Department at the Hamamatsu Plant when it lost its only contract for passenger vehicle seats 10 years ago. I can clearly recall our deep disappointment. I took on this project with a firm commitment to regaining the customer’s contract, one way or another. As you can’t win back a lost contract through run-of-the-mill efforts, on this project we made more proposals than ever before to better reflect the customer’s point of view.
SakuraiIn particular, we focused on our approach to the customer’s chief engineers responsible for model development. While we had opportunities before to meet and talk with the staff in procurement and interior design sections, the chief engineers had always remained out of reach. Previously, therefore, we made our proposals through the customer’s representative staff, but we never knew if they had adequately communicated the true goals of our proposals, as well as our enthusiasm, to the chief engineers. This time, we wanted to ensure the development concept of the seats, which we had been developing in advance, was effectively communicated, and the Hamamatsu Plant had staked its reputation on this. Relying on various network connections with the customer, we finally got to meet the chief engineer for the first time.
We used this opportunity to present numerous technological proposals based on our proprietary market research and advanced development. When the chief engineer showed an interest in the specifics, we followed up with an invitation to our Technical Center in Tochigi Prefecture (Fig. 1), where we gave a comprehensive demonstration of our technological capabilities. “I’m surprised to see a parts maker doing such advanced R&D like this,” the chief engineer commented. We ended up securing opportunities for a succession of proposals. Ultimately, by carefully listening to the customer’s needs and responding to them in full, we won the contract.
How did you meet the customer’s needs?
AidaThe customer’s first request was for more convenient seats. On previous models, the rear of the folded seats (the storage compartment floor) had been inclined slightly. For the new model, we developed seats that folded up into more compact dimensions. To do this, we modified the shape of the joint used to fold the seats. This resulted in a flat storage compartment floor. It also increased the height of the storage compartment by 40 mm and made it significantly easier to load items like bicycles or large cargo (Fig. 2).
The multi-use flap created alongside Suzuki’s development staff significantly improves convenience. For improved comfort, the flap can serve as a leg rest (Fig. 3). A new feature allows the flap to be positioned upright as a cargo stopper. Used with the armrests added to rear seats for the first time with this model, users can secure cargo in four directions: fore and aft, left and right. This makes the rear seats ideal for both seating and safe cargo storage (Fig. 4).
MatsushimaAnother thing that made this project unique was by approaching development based on sharing ideas with the customer on various specifications on everyday use, like covering the flap in a material that is easy to wipe clean. Combinations of ideas like this from both companies made it possible to develop a highly finished seat design we believed would be certain to delight end users.
TakahashiWe focused in particular on the feel of sitting in the seats, an essential aspect when talking about comfort. In the development process, we needed to reduce seat thickness to allow smoother and more compact stowage. At the same time, since the seat contained the multi-use flap, we couldn’t use urethane pads of the same thickness as previous models. This led to concerns about less comfortable seating. But through repeated testing with the materials maker, we were able to improve the ingredient ratio and other factors and develop well-balanced urethane pads that provided soft, supportive, comfortable seating.
Another challenge was combining the structural components of this multipurpose seating within the limited space of the seat itself. We needed to incorporate into this compact seat not just the components for seat sliding and stowage but also those for flap angle adjustment and extension and retraction. Through repeated testing with the Design Project Leader, we created an optimal interior structure. It was like assembling a jigsaw puzzle.
AidaThe multi-use flap embodies our attention to comfort. In fact, in the early development stages, the flap was larger, but along the way we made it more compact since the larger version hit the floor when you stowed the seat. But just reducing the size of the flap would result in a less comfortable seat, and for certain physiques it would poke into their calves. So, we developed a new structure where the flap itself extends and retracts. This resulted in a more comfortable seat that didn’t dig into the calves (Fig. 5). It’s an example of the uncompromising approach we took not just for the rear seat convenience and functionality of the new Spacia, but also regarding our company’s core value of comfort.
Simply shortening the flap results in painful poking of the leg.
A structure of adjustable length which provides partial leg support and improved comfort
MatsushimaWe were able to pursue this development project in partnership with the customer, which led to developing seats that would deliver greater satisfaction to more end users. I felt honored that we had received such a positive reaction from the press and social media for our efforts. The start of mass production clearly enlivened the Hamamatsu Plant, and the customer has since enquired about future projects. We’re committed to delivering delight and satisfaction to global markets through an approach of continually improved manufacturing to better reflect customer needs.