Mar. 18, 2024
Introduction of new models
Creating a high-quality cabin interior that goes beyond the standard grade
Honda CIVIC
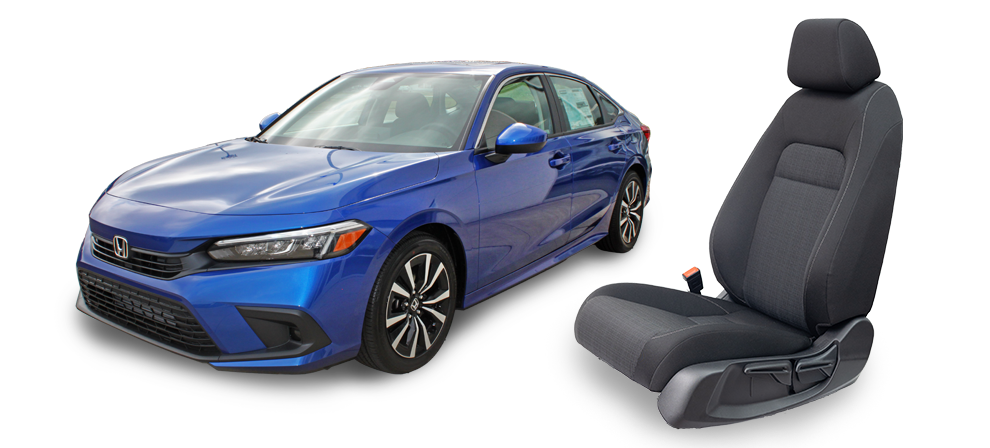
Ever since it was first released in 1972 as the "global basic car,"
the Honda Civic has been beloved both in Japan and around the world.
The 11th generation Civic, which underwent a full model change,
was released in the United States in June 2021.
We asked project members to tell us the story behind the development of
the seats and door trims that were installed in the latest model.
Profile
-
Naoto Sayama
Model LPL Office
LPL (Large Project Leader)
Joined TS TECH in 1987. Assigned to the Design Department before being posted to the U.S. in 2001. After returning to Japan in 2009, worked on and led projects for various models as the LPL.
-
Yuta Kijima
Design Department
Design PL(Project Leader)
Joined TS TECH in 2010. After joining, was involved in development projects for the 9th and 10th generation Civic. Served as Design PL for the seats in the new 11th generation Civic.
-
Takuya Hara
Design Department
Design PL (Project Leader)
Joined TS TECH in 2013. After joining, was in charge of door trim designs. Served in his first role as a Design PL for the new Civic.
-
So Iwakata
Product Engineering Department
Prototype Staff
Joined TS TECH in 2001. Moved from the Vehicle Sales Department at the Hamamatsu Branch to the Product Engineering Department. Has subsequently been in charge of prototypes as part of seat development and involved in seat prototypes during the development of various models.
-
Shunichi Sakurai
Model Control Department
Production Line Planning Staff
Joined TS TECH in 2014. Assigned to the Model Control Department. Helped streamline production line processes for the new Civic.
*Departments and positions current as of time of interview
What type of seats did you set out to develop?
Sayama:The Civic is a global model that is the pride of our customer (Honda). As the seats are manufactured in many locations around the world, they need to have reproducibility to ensure that they are made with the same high level of quality, regardless of where they are made. Even if prototypes have a high-quality finish during the development stage, our efforts are meaningless if the same level of quality cannot be reproduced after starting mass production. With this in mind, we set out to produce high-quality seats and door trims with a high level of reproducibility.
After mass-production begins, it is the plant workers who make the seats. The first thing we thought of in order to achieve the same finish around the world without the use of special technology or tools was to minimize the "effort" required by those workers. Rather than relying on the workers' skills to achieve a quality finish, we focused on the design stage as a way of reducing the amount of "effort" - in other words, the "number of work hours" - required at the plant, and boost reproducibility to achieve a high-quality finish with simple steps. This not only results in raising the quality of products but also prevents defective work during the production process, which can help limit mass production costs. The Civic is a "global basic car" that almost anyone can afford. I think that our efforts also played a role in making the model more cost competitive.
Creating "exterior elegance" that exceeds that of previous models was also another development concept. We were just as keen as our customer when it came to the exterior appearance, so we actually visited our customer's R&D center during the initial stages of development before the design of these seats was even finalized. Honda designers and our project members were able to work together to come up with initial designs and, as a result, created an elegant-looking design that also had a high level of reproducibility, which allowed subsequent development to progress smoothly. This approach had never been used in past development processes, and in turn this led to a greater level of anticipation by the customer.
What ideas did you incorporate to achieve the elegant look and high level of reproducibility?
KijimaThe new Civic features the next-generation seat frame that our company developed. This is our core frame that can be used in seats for a broad range of models, from compact cars to luxury sedans, and it was developed to be easier to sit in, make driving easier, and prevent fatigue.
With the large number of plants producing the first run of seats using this frame, we invited about 40 staff members in charge of production at plants around the world to a review session held at our Technical Center in Japan. During the session, we identified difficulties staff members had during production of the previous model and examined those trouble spots using the actual product. Their feedback was then applied to samples during the session through repeated assembly and disassembly of the seat. While the review session was relatively short at one week, the feedback we received provided excellent hints during the course of development for improving the production reproducibility and efficiency.
To achieve an elegant look, we focused on the design of the urethane pads inside the seats. During the manufacturing process, we cover the surface of these urethane pads with leather or fabric (called the trim cover). The pressure applied during this process can cause the urethane pads to become squashed or pushed to one side, which makes them look twisted. To address this, we incorporated ideas during the design stage, like increasing the urethane thickness in areas that become squashed easily or reducing the thickness of the urethane in areas that are pushed to one side, so we could achieve a look that was closer to what the customer wanted. The shape of the urethane pads is normally refined over the course of development, but with the new Civic we worked on this from the early stages so we could achieve design lines that were as close as possible to the ideal shape the customer wanted, rather than design lines that they deemed acceptable. Naturally, prototypes can also be updated to achieve the ideal look that the customer is trying to achieve, and minor tweaks to the appearance that are not noticeable with the 3D data can be verified using the actual product so that minute modifications are made until the final elegant look is achieved.
IwakataWe have incorporated our ideas into the trim cover as well. In addition to the frame and urethane pads, the seat also houses airbags and many other electronic components. If the stitching of the trim cover that encases all these components experiences even just a slight shift, it will result in wrinkles forming during the assembly process.
To prevent this from happening, we spent a lot of time testing different shapes of paper templates - the design drawings for the trim covers - so that the same finish can be achieved regardless of who sewed the trim cover. To improve the reproducibility, the position of the sewing points (Fig. 1) that serve to indicate where surface material is sewed together is crucial. Until now, this had been measured manually by the worker, but for the first time we used CAD* for paper templates so we could test the set positions and ensure that the sewing points of each paper template and the edges of the templates lined up perfectly. This meticulous attention to detail for the templates is what led to the high quality of the final product.
*CAD: Design tool aided by the use of a computer
The sections marked with ● are examples of sewing points. A number of points are located behind each seam, although they are not visible in the final product.
This attention to detail through the templates is also applied to the seat surface and leads to an even more elegant finish overall.
KijimaNaturally we sought more than just an elegant look - neck area protection (ensuring the safety of occupant neck regions during collisions) and a comfortable feel when driving were also important, so we focused on enhancing all three of these aspects. The use of the next-generation seat frame provided a reliable baseline for comfort and safety, so the shape of the urethane pads was vital to enhance these qualities even further.
In the event of a collision, securing occupants quicker and deeper in the seat helps to protect their neck area, so the seats need a certain degree of flexibility. To achieve this, the number of holes and grooves in the urethane pad can simply be increased but doing that would just result in the urethane pad being squashed to the side where the holes are, which would adversely affect the appearance. The same applies when trying to make the seats comfortable; Reducing the urethane pad to improve the seating comfort would result in twisting to that side. We are faced with dilemmas like this all the time, but as we had an idea of the ideal design lines from the initial stages of development, making minor adjustments to the urethane pad was a smooth process. Keeping the final appearance in mind during development meant we could achieve both safety and comfort, and as a result I think we contributed to achieving the "comfortable" concept of the new Civic.
HaraA lighter weight that leads to better fuel efficiency and the all-important safety were two key aspects we kept in mind during development. We can achieve a lighter weight by making parts thinner, but simply making them thinner also reduces their strength. To overcome this, we suggested using a lattice shape on the reverse side of the door trim for the new Civic. This lattice shape actually increases the strength of parts and helps to prevent deformation and damage, so the parts can be made thinner and lighter in weight. We analyzed the strength and safety over and over again using CAE* and came up with a design that met all weight, strength, and safety requirements. We were overjoyed, as the customer also praised the design.
This was the first time that cushions were included in the door trim armrests of a Civic. We spent a lot of time altering the thickness and material in order to achieve the level of softness and feel required for the cushions. You will no doubt be able to feel how comfortable the cushion is when you rest your arm on it.
*CAE: A system that uses computers to run simulations of designed products.
SakuraiWe also had to incorporate ideas into the door trims to increase reproducibility during mass production. I was in charge of making manufacturing lines more efficient. Reducing the effort required by workers helps to increase reproducibility. An example that highlights this is the number of resin parts that need to be assembled during mass-production to make up the final door trim. Previous designs had parts that were installed on either the front side or rear side, but we were able to reduce the number of work hours required for assembly by having all parts installed from a single side. While this is just one example, including ideas like this here and there helped to streamline the total work hours required for assembling the door trims by around half compared to conventional assembly lines.
Yet all this would be meaningless if quality suffered as a result of greater efficiency. In addition to improving assembly efficiency, we included many ways to create a better-looking finish using simple procedures. Increasing the molding accuracy of each part from the design stage helps to achieve a higher quality finish, even as assembly processes become more efficient.
After the completion of this project
The difficulties faced working on this global model and the growth from overcoming challenges will become the backbone of future manufacturing efforts
SayamaVarious departments including Development, Production, Sales, Purchasing, and Quality Control worked together on this project, and we all focused on development as a single team. With the Civic being a global model, staff from sites around the world helped out to provide us with a broad range of ideas and feedback. In addition to our own staff, we held meetings with countless suppliers and manufacturers to discuss aspects related to each individual part. The fruits of this far-ranging level of cooperation are the newly developed seats and door trims. As a result, I believe that we have made a product that we can proudly say is a "global standard." Being a global model, we had to come up with a manufacturing solution that factored in sites around the world, not just those in Japan. We not only had to cover the design, but all aspects related to procurement, costs, and production systems, and this proved to be a valuable experience for all project members to learn more and grow. As they go on to lead projects for other models, everyone involved in this development can be certain that their experience will help further enhance our manufacturing capabilities so we can make even better products in the future.