Mar. 18, 2024
Introduction of new models
Setting a new standard for the world’s No. 1 ride quality
Honda CIVIC
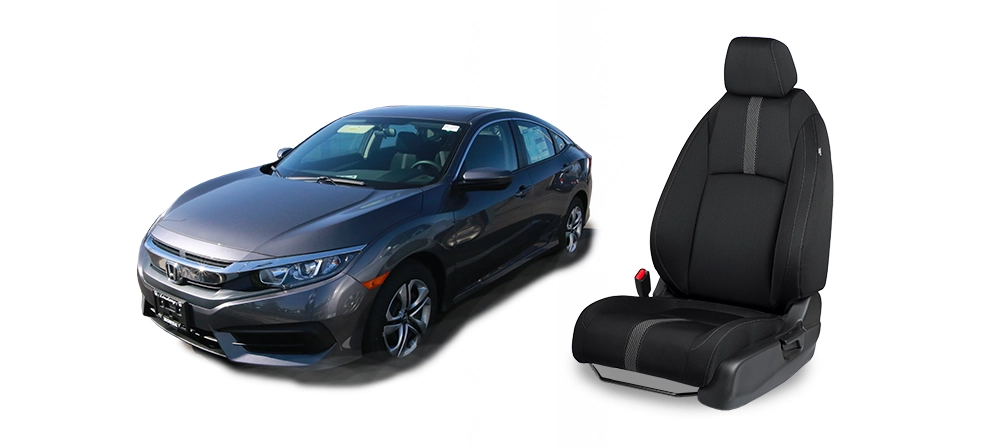
We asked project members about the development process for the seats and door trim installed in the new, tenth-generation Honda Civic, which was created as a benchmark for compact-class cars.
Profile
-
Masahiro Nakamura
TRIMOLD LLC Chairman
TS TRIM INDUSTRIES INC. PresidentNakamura joined the Design Department of the company in 1985 as a designer of interiors and steering systems. He later became a Large Project Leader (LPL) after serving as manager of the Development Administration Section. Since 2015 he has been stationed in the U.S. as the president of a manufacturing subsidiary. He participated in this project as a global LPL.
-
Masaji Machii
Executive Chief Engineer
Machii joined the company’s Design Department in 1982 as a designer of seats. He became an LPL in 2010. Since 2013 he has been stationed in the U.S. as a design supervisor for a research department. He joined this project as an LPL in North America after the development transfer.
-
Jim Denlinger
Chief Engineer
Denlinger joined the Design Department of TS TECH AMERICAS, INC. in 2003 to support the development of seats for North American models. He participated in this project as a Development Project Leader (DPL).
-
Koji Yasui
Assistant Chief Engineer
Yasui joined the Design Department of TS TECH AMERICAS, INC. in 2006 as a designer of interiors. He was responsible for the development of the door trim during this project.
NakamuraThe Civic is a well- known model that is sold all over the world. Many outstanding companies competed in the heated contest to win the bid. But the Civic was an especially important model for our company: we simply had to win. It was a huge challenge to work out a cost proposal competitive enough to guarantee us success.
The development of the new Civic began in Japan but was later transferred to North America to better respond to the needs of the U.S. market, a major market for the model, and end user opinions. Our own development work was transferred to the U.S. at the same time.
Looking back at my work on the project as an LPL, I remember the many headaches the transfer caused for associated departments. The chaos and development setbacks during the transfer cost me a lot of sleep.
We wanted to address three main customer demands in the development of the new Civic. The first was cost. Next was a marked reduction in weight in order to surpass the fuel efficiency of the former model. Finally, we wanted to achieve the world’s number one ride quality. The comfort of the seat, of course, plays a huge role in ride quality. Our challenge was to design an incredibly comfortable seat without deviating from our cost and weight targets.
MachiiThe needs for a seat vary from one country or culture to the next. This translates into large differences in the design philosophy. The Japanese, for example, prefer firmer seats, while Americans are partial to a softer, cushier feel. Their preferences are determined in part by their physiques.
Our mission is to design a seat that satisfies as many people as possible in a vehicle sold all over the world. Our success in meeting different regional demands within the budget limits hinges on our local development know-how in the markets and regions where we sell.
NakamuraWhen we transferred development to North America, we had to reflect to an even greater degree the local needs for ride quality and other key design points. This required a change in the basic design philosophy behind the development we had already completed in Japan. From the outset, every single design and specification was decided for a purpose. Nothing was left to chance. So the sudden modifications for the new market posed huge challenges. We also had to consider needs and production costs in different countries, as the Civic is a global model. We really had to rack our brains.
Eventually we found solutions using state-of-the art technology for the frame and urethane as a cushioning material. We used our know-how for reducing passenger and driver fatigue from extended periods of sitting to design a frame and seat contours that enhanced ride quality. We then adjusted the softness of the seat to suit the preferences of passengers in different parts of the world.
NakamuraOne of the reasons that the Civic is an important model for us lies in the frame used for the seat. Instead of the standard Civic frame from earlier models, we adopted the slightly larger “global standard frame” to improve component competitiveness. Our design decisions for the frame in the current model are likely to be modified in future models, to change as the Civic changes generation by generation. So our development work in the present will have a huge and lasting influence.
In developing the new-generation “global standard frame,” we placed high importance on the minimization and standardization of parts in order to drastically reduce cost and weight and enable better expandability to other models. The frame structure, for example, largely depends on whether the seat position is adjusted electrically or manually. We therefore created a design to minimize the structural differences and adopted an inexpensive, lightweight frame with better strength and safety functions compared to the conventional frame. We also worked out flexible specifications to enable added functions and new modifications in future models without requiring major development work.
On the production side, we reduced costs by introducing the latest integrated welding to greatly improve efficiency, laser welding to dramatically improve processing speed, and a fully automated system for welding quality inspection.
These modifications allowed us to manufacture power seats, typically an expensive product, at low cost. More passengers can now ride in greater comfort and class as a result.
DenlingerA new requirement known as the “limit rear end collision strength” was applied to the new Civic to mitigate rear collision injury. Coupled with the weight requirement, this resulted in a considerable challenge for us. We repeated thorough CAE analysis and examinations and ultimately raised safety beyond the levels achieved in the former model.
We were also particular about improving the convenience of specific parts. We designed a height adjustment mechanism that matched handle load vs height climb relative to the number of lever adjustments, and we inspected it repeatedly using optimization software to ensure easy use for passengers.
NakamuraWe were also particular about the door trim. We came up with a truly sleek, attractive design. (Smiles)
When the previous generation was released, a professional journal published by an American consumer organization discounted it as totally cheap. Of course we upgraded the trim with the model change to the Civic, but I think we were also spurred by the progress of other companies in developing rapidly improved textures.
YasuiMost users seem to instantly notice the improved texture of the door trim for the new Civic compared to the previous generation.
We try to impress users with the luxury of the interior when they get in the car, mainly by adding decorative parts* such as metallic finish. To avoid the high costs of conventional development, we introduced a full-scale “sample-less” style of development using design and simulation software to reduce inspections of actual prototypes. This new approach considerably lowered development costs and improved development speed in the production of the global model Civic.
*Decorative parts: parts for decoration to enhance the appearance of the interior.
MachiiThe Civic was the first model in which the next-generation “global standard frame” was installed. The project therefore required extensive coordination with the customer and the production side of the company. The local staff had a very hard time satisfying the many requests. Thanks to the tremendous effort by Jim, the tasks were somehow completed.
DenlingerI met with the customer almost every day. Time and time again, the customer asked us to change the specifications for the ride quality of this model. We had to make adjustments up to the very last moment before mass production.
The customer and the design departments of our companies in America and Japan all have their own ideas. It took a lot of effort to settle on a design that made everyone happy. We had a particularly tough time with the frame in terms of matching the ideas with the design. The design philosophy drastically changed when we changed the development location.
NakamuraThe seat for this project had very lofty goals. It wasn’t easy to achieve the customer’s requests and our own targets. It was a critical situation, and, as I said earlier, the disruption by our transfer to North America cost me many nights of sleep. (Wry smile)
Every day I fought against unexpected challenges. Once when I flew from Japan to the U.S. to get an approval from the customer (a designer), the customer asked me to make a quick specification change to achieve the targets. We were practically making the molds by then, but the customer insisted on the change. There were far too many problems for me to relate to you here.
Within the limited development period we built a development system unlike anything else we ever achieved, thanks to the efforts of Jim and the local staff and abundant support from Japan. We staked the future of our company on this project, and we succeeded in one challenge after another.
After the project
The more the challenges there were, the better the product became
NakamuraUnlike our previous experiences, we had to cope with so many irregular situations and tasks. Thankfully, through quick decision-making and effective, flexible work, we managed to cope. The support between Japan and the U.S. progressed smoothly. The project members sometimes took issue with my various tough requests and demands, but they ultimately came through and did what we needed. I really appreciate their efforts. Ultimately they further refined their skills.
MachiiIt was the first time we developed a main model in the U.S., but the local staff worked just as hard on it as they would on any other project. I’m also thankful to them for their efforts. We made a good product in spite of the many difficulties we faced, such as the development transfer and specification changes. The new Civic received the Car of the Year in North America and enjoys a good reputation. I believe our products contributed to the model’s success.