Production structure
Global management structure to realize production of consistent quality worldwide
TS TECH has developed a regional headquarters structure to enable close cooperation between regions while enhancing its systematic production supports under a global management structure from the global production headquarters in Japan.
From the product planning stage, wide-ranging information including market needs from global facilities are consolidated in Japan, where product specifications and production methods are precisely defined before rapid lateral deployment worldwide. This results in a structure that minimizes losses and promotes the stable production of high-quality products.
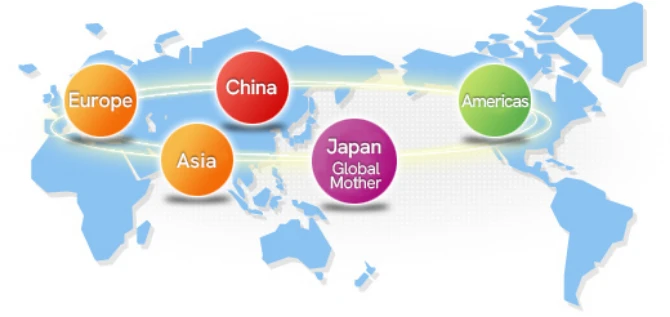
Strong production technology capabilities to generate flexible production structures
Production technology sections are also involved from the initial development stage to achieve quality targets for each product, incorporating methods and process designs to generate stable quality. TS TECH's production technologies and expertise are fully demonstrated in processing technologies, assembly technologies, and other areas.
Our achievements in the production field include assembly lines that smooth out workload fluctuations between individual products, reliable QA systems for individual processes, and flexible line structures capable of handling various types of vehicles. Our production structure is both highly efficient and resistant to production fluctuations.
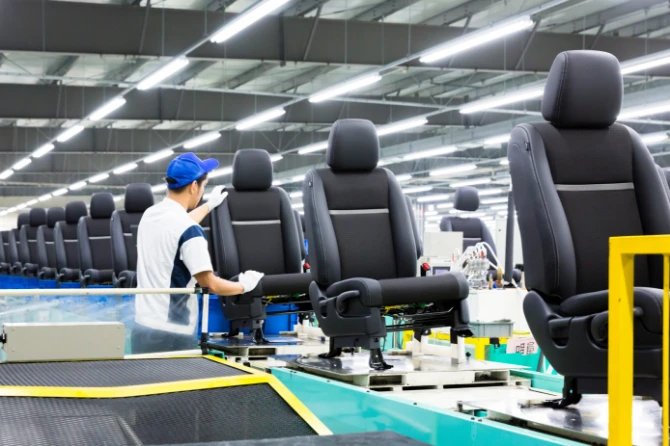
Automated production lines that put robotics to effective use
We deploy industrial robotics to achieve fully automated production for processes ranging from seat frame welding to assembly. Even in seat production, in which the use of parts made of different materials often presents challenges for automation, we maximize production efficiency by deploying robotics equipment that meets optimized specifications on our lines.
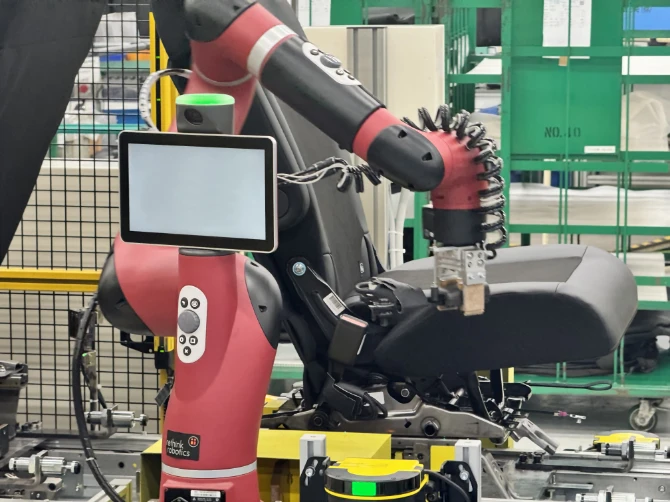
Imaging and finished product inspections
After joining and welding parts, we employ imaging inspection using precision cameras to detect defects in individual processes and to ensure that no defective units are passed down the line. The final stage on the main line is a soundproof testing room, where we strictly check on the sound when actually seated in the seats in addition to conventional external and functional inspections.
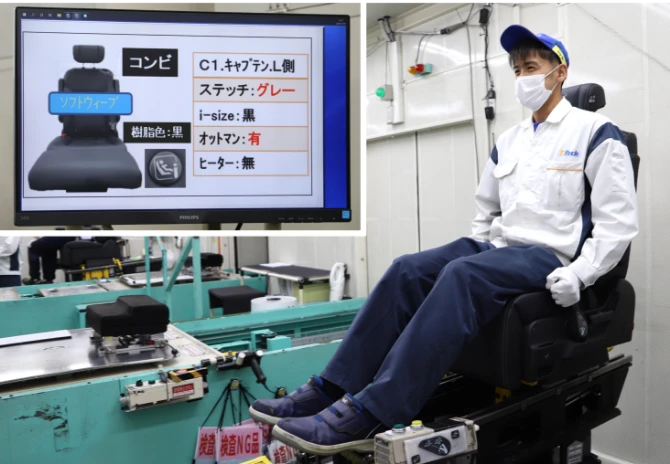
Thorough QA in each product production process
TS TECH is building production lines aimed at in-process QA. Each assembly line is equipped with tools and equipment for work assurance and testing equipment at key points, to enable thorough process quality control. We realize more reliable QA through this system that ensures that only quality products make it to the next stage.
We also use bar codes for traceability of key parts.
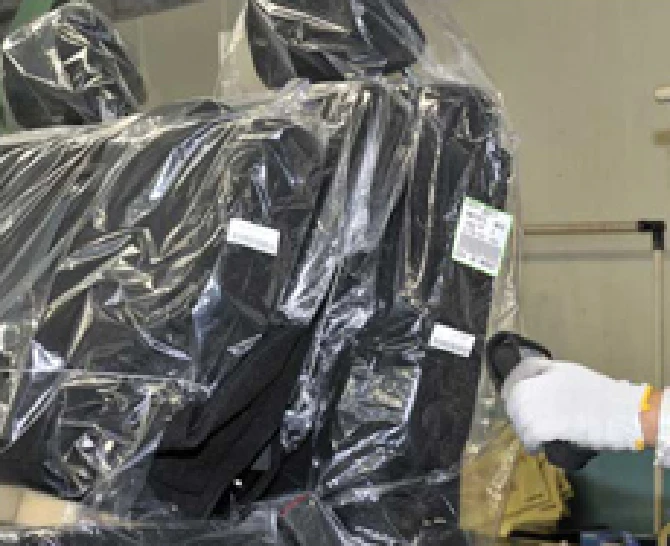
Minimizing product inventories through direct deliveries based on synchronized production
We minimize inventories by creating production plans leveled using our own proprietary process based on customer production schedules. Products produced on each production line are sorted by shipping equipment to match customers’ production schedules and then loaded on trucks for delivery to customers directly through synchronized production.
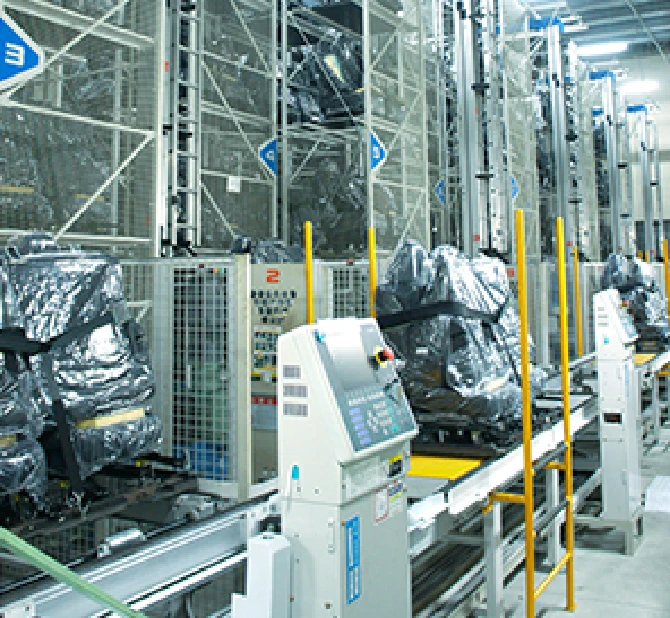