2024年03月18日
新機種紹介
スタンダードの枠を超えた
上質な車室空間を演出
Honda CIVIC
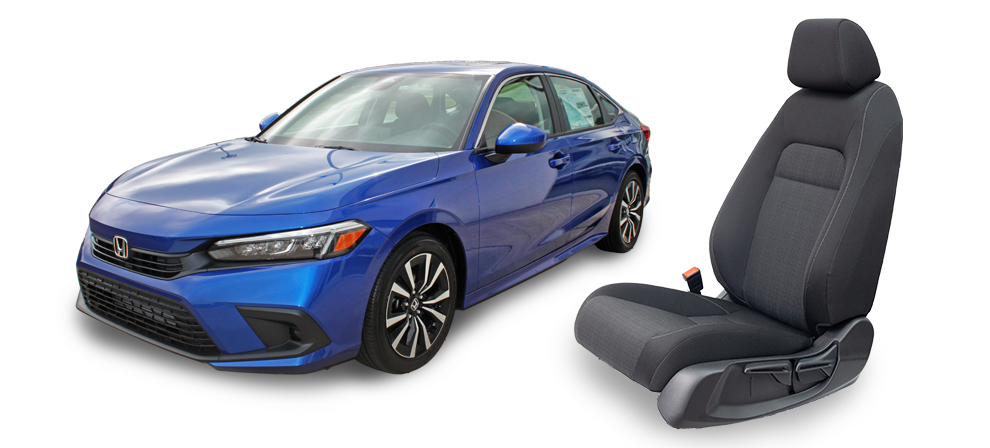
1972年「世界のベーシックカー」として誕生して以来、
日本はもちろん、世界中で愛され続けるHonda 「CIVIC」。
2021年6月、フルモデルチェンジにより11代目「CIVIC」が米国で発売されました。
これに搭載された当社製シートとドアトリム(ドアの内張り)の開発秘話を、
プロジェクトメンバーの皆さんに伺いました。
Profile
-
佐山 直人
機種LPL室
LPL(ラージ プロジェクト リーダー)
1987年入社。設計部門に配属後、2001年からアメリカに駐在。2009年に帰国以降、LPLとしてさまざまな機種を担当し、各プロジェクトを主導する。
-
木島 裕太
設計部
設計PL(プロジェクトリーダー)
2010年入社。入社当初から9代目、また10代目とCIVIC開発プロジェクトに携わり、11代目となる新型CIVICではシートの設計PLを担当。
-
原 拓也
設計部
設計PL(プロジェクトリーダー)
2013年入社。入社当初からドアトリムの設計を担当し、新型CIVICでは自身初となるドアの設計PLを担当。
-
岩片 創
製品技術部
試作担当
2001年入社。車輌販売部浜松営業所から製品技術部に異動。以降、シート開発における試作を担当し、数々の機種開発でシート試作を手掛ける。
-
櫻井 竣一
機種計画部
製造ライン企画担当
2014年入社。機種計画部に配属。新型CIVICでは、製造ラインでの工程効率化を推進。
どのようなシートを目指して開発されたのでしょうか。
佐山CIVICはお客さま(Honda)が誇るグローバルモデルの一つです。そのシートは、世界中で生産されることから、どの工場でも高品質な製品を造り出せる再現性が求められます。開発中の試作品ではきれいに仕上がっていても、量産開始後、その仕上がりを再現できないのでは意味がありません。そのため、シートもドアトリムも、高品質で再現性の高い製品の実現を目指しました。
量産が始まれば、造るのは工場で働く現場の方たちです。世界中、特別な技術や道具がなくても、同じ仕上がりとするためにまず考えたのは、彼らの「手間」をいかに省くかです。上質な仕上がりを彼らの手だけに委ねるのではなく、設計段階から徹底した現場の「手間」、いわゆる「作業工数」の削減を追求することで、簡単な作業で上質な仕上がりを生み出す再現性を高めました。これは、製品品質の向上だけでなく、製造工程での加工不良の発生を防ぐ効果もあり、量産コストの抑制につながっていきます。CIVICは一般の方でも手が届きやすい「世界のベーシックカー」です。私たちの取り組みは、その価格競争力の創出にも一役買ったのではないでしょうか。
さらに、先代モデルを超える「製品外観の美しさ」も開発コンセプトの1つとなっています。外観にかける強い想いはお客さまとも共有していたため、今回はシートデザインが決まる前の開発初期段階からお客さまの研究所へ足を運びました。デザイナーと当社プロジェクトメンバーが一体となって初期構想を練ることができた結果、外観の美しさと再現性を高いレベルで両立したデザイン案が生み出され、その後の開発を円滑に進めることができました。従来の開発ではそのような進め方をすることはなかったので、それだけお客さまからの期待も高かったのだと思います。
外観の美しさや再現性を高めるための工夫を教えてください。
木島新型CIVICには、当社が開発した次世代シートフレームが搭載されています。これは、コンパクトカーから上級セダンまで、幅広い車種をカバーすることができる当社の主力となるフレームで、「座りやすさ」「運転しやすさ」「疲れにくさ」にこだわって開発されました。 このフレームを使ったシートを初めて生産する工場も多く、開発初期段階で、世界各国の工場で実際に生産を担当する約40名を日本の技術センターに集め、検証会を行いました。検証にあたっては、前モデルの生産時に苦労した点を現物で確認を行いながらヒアリングし、皆さんの声をその場でサンプル品に反映しては組み立てと分解を繰り返しました。検証期間は約1週間と短かったものの、この検証で得た“生の声”は開発を進めていく上で、量産時の再現性や生産効率を高めるための強力なヒントになりました。
また、外観の美しさを実現するため、シートの中にあるウレタンパッドの設計に力を入れました。製造工程では、ウレタンパッドに表面を覆うための皮革や布(以下、トリムカバー)を被せていくのですが、その際、圧力がかかることで、ウレタンパッドがつぶれたり、片寄ったりすることで外観にゆがみが生じます。それを防ぐため、つぶれやすい箇所にはウレタンを厚めに盛り、片寄りが生じる箇所のウレタンは削るなど設計段階から工夫を凝らし、お客さまの求める外観へと近づけていきます。通常、開発を進めるにつれてウレタンパッドの形状を仕上げていくのですが、新型CIVICでは、開発開始当初からこの作業に取り組んだことで、お客さまが“許容できる”デザインラインではなく、“理想”とするデザインラインに限りなく一致させています。当然、試作品にも理想の製品外観を目指した造りを反映でき、3Dデータでは分からない現物ならではの外観のわずかなゆがみをチェックし、さらに細かく修正できたことが、最終的な外観の美しさにつながっています。
岩片トリムカバーにも工夫をこらしています。シートの中には骨格となるフレームや、ウレタンパッドなどの他、エアバックやさまざまな電装部品が組み込まれているため、それらを覆うトリムカバーの縫製に少しでもズレがあると、組み立て時にシワやゆがみが生じてしまいます。
これを防ぐため、トリムカバーの設計図ともいえる型紙の作成時、誰が縫っても同じ仕上がりとなるように何度も試行錯誤を繰り返しました。再現性を高めるには、表皮を縫い合わせる際の目印となる縫製ポイント(図1参照)の位置が重要となるのですが、これまで人の手で計測していたのに対し、今回初めて型紙専用CAD※を導入し、設定箇所の検証を重ねることで、縫い合わせる型紙同士の縫製ポイントや型紙の端を完全に一致させることができました。こうした緻密な型紙設計が、高品質な製品につながっています。
※CAD:コンピューターによる設計支援ツール
●が縫製ポイントとなる部分の一例。完成した製品からは確認できないが、縫い目の奥にはいくつものポイントが設定されている。
こうした型紙へのこだわりは座面にも反映され、全体の仕上がりの美しさへとつながっている。
木島もちろん、外観の美しさだけでなく、頸部性能(首部分の衝突時の安全性)や運転時の快適なフィーリング、この3点全てを高い次元で実現することにも注力しました。次世代シートフレームの採用により、快適性や安全性の土台はできていたので、それらの性能をさらに引き上げるには、ウレタンパッドの形状が重要でした。
衝突時に乗員を、より早く・より深くシートに押さえつけることで頸部性能は確保できるので、シートにはたわみやすさが求められます。そのためには、極端に言えば、ウレタンパッドに穴や溝を増やしてしまえばいいのですが、そうすると今度はその穴の方にウレタンパッドが片寄ってしまい、外観が崩れてしまいます。フィーリングを調整する際も同様で、座り心地を求めるあまりウレタンパッドを削りすぎてしまえば、そこにゆがみが生じます。そうしたジレンマは必ずあるものですが、開発当初から理想のデザインラインを意識したことで、ウレタンパッドの微調整を円滑に進めることができました。こうして外観にこだわって開発を進めたことで、安全性と快適性が両立でき、結果として新型CIVICのコンセプトである“爽快さ”の実現にも貢献することができたのだと思います。
原低燃費につながる「軽量化」と、何よりも大切な「安全性」の両立を強く意識しました。一つひとつの部品を削って薄くすれば軽量化にはなりますが、単純に薄くするだけでは、強度が低下してしまいます。そこで、新型CIVICでは、ドアトリム裏面の形状を格子状にすることを提案しました。格子状にすることで部品自体の強度が上がり、変形や破損を防げるため、部品をさらに薄くし、軽量化につなげることができています。CAE※で強度と安全性の解析を繰り返すことで、重量・強度・安全性の全てを満足するものができましたし、お客さまにも良い評価を頂いたので、うれしかったですね。
また、CIVICとしては初めてドアトリムのアームレストにクッションを設けていますが、クッションに求められる柔らかさやフィーリングに合わせて、入念に厚みや素材の調整を行いました。実際に手を置いたときにはその快適さを実感していただけると思います。
※CAE:コンピューター上で、設計した製品のシミュレーションを行うためのシステム
櫻井ドアトリムについても、量産時の再現性を高めるための工夫を行っています。私が担当したのは製造ラインの高効率化です。作業者の手間を省くことで、再現性の向上につなげています。例えば、ドアトリムは複数の樹脂部品から構成されるのですが、量産時はそれらを一つひとつ組み付けて形にしていきます。従来ですと、表、裏、それぞれの面から取り付ける部品があったのですが、一方向から取り付けられる部品に統一することで、組み立て工数の削減を行っています。これはあくまで一例ですが、こうした工夫を一つひとつ積み重ねていくことで、ドアトリムの組み立て工程に必要な作業人数を、従来のラインに比べて約半分に減らせるほど効率化することができました。
ただ、効率化を求めるあまり、製品品質が落ちてしまっては元も子もありません。組み立て効率を向上させるだけでなく、より簡単な作業で美しく仕上がる工夫も各所に施しています。また、各部品の設計段階から成型精度を高めることで、効率化が進む組み立て工程においても美しい仕上がりを実現しています。
プロジェクトを終えて
グローバルモデルだからこその苦労と、乗り越えた先にある成長が
次のモノづくりを支える
佐山今回のプロジェクトでは、開発、生産、営業、購買、品質管理など、さまざまな部門が協力し合い、チーム一丸となって開発を進めました。特に、CIVICはグローバルモデルということもあり、世界中の拠点の皆さんにもご協力いただき、たくさんのアイデアやご意見を頂きました。また、社内だけではなく、多くの取引先メーカーの皆さまとも部品の一つひとつで打合せを重ね、ご協力いただきながら完成まで漕ぎつけたのが、今回のシートとドアトリムです。その甲斐もあって、「これがグローバルスタンダードだ」と胸を張れる製品が出来上がったと自負しています。
また、グローバルモデルであるからこそ、日本だけでなく、世界中の拠点のことを考えたモノづくりが求められました。設計はもちろん調達やコスト、生産体制に至るまで全体を見渡す必要があり、プロジェクトメンバーの皆さんにとって、大きな学びと成長の機会となったのではないでしょうか。この経験をした皆さんが、またそれぞれ違う機種を担当していくことで、当社のモノづくりは進化を続け、より魅力的な製品を世に送り出すことができるものと信じています。