開発体制
主な開発の流れ
-
STEP 01
調査・先行企画
自社の製品位置づけを明確にするために、市場調査などを実施。調査に基づいた競争力ある提案を検討します。
-
STEP 02
企画提案
自動車メーカーから提示されるコンセプトに基づき、自社調査・検討の結果を踏まえた企画提案を行います。
-
STEP 03
設計
CADを使って、当社が独自に設計を行います。設計データは各部門の意思を反映しながら熟成させていきます。
-
STEP 04
CAE解析
CAEを駆使して、試作品を造る前に、製品の加工法や構造、材料などの解析評価を行い、図面を熱成します。
-
STEP 05
試作研究
CAE解析で充分に精度を高めたうえで試作品を製作し、より造りやすい仕様や、商品性の向上などを検討します。
-
STEP 06
衝擊試験
ダイナミック試験機を使って精度の高い衝突試験を実施、製品の安全性能を実証します。
-
STEP 07
耐久・性能試験
製品そのものの強度耐久から、あらゆる環境下での耐久や性能評価まで、幅広い試験を実施します。
-
STEP 08
評価(レビュー)
製品の設計仕様はさまざまな観点からり返しレビューされ、抽出された課題は関連部署へフィードバックし、改善された上で承認されます。
独自性と高い競争力を持った商品開発を実現するLPL体制
新機種の開発において、テイ・エス テックは「LPL体制」を導入しています。これは、海外拠点も含めた各部門を取りまとめるLPL(ラージプロジェクトリーダー)を配置し、企画立案から量産までをトータルにマネジメントするものです。LPLが顧客窓口となり、各部門をリードしながら、当社独自の競争力の高い魅力ある製品の開発を行っています。
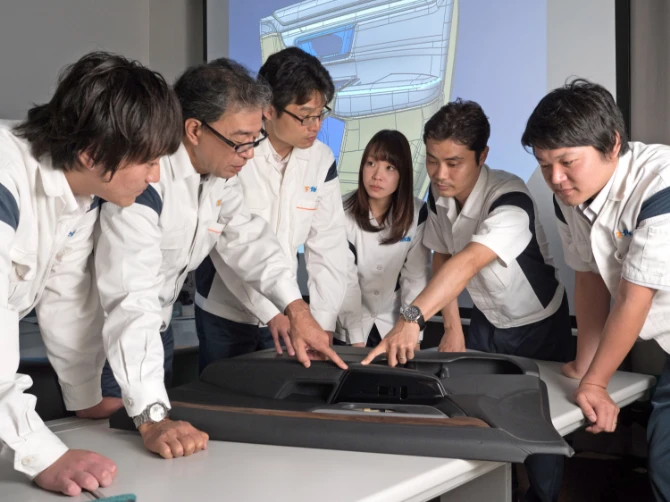
徹底した素材評価
より質の高い製品をつくるために、テイ・エス テックは素材評価を行っています。布地、樹脂、ウレタン、鋼材、接着剤など、製品を構成する原材料を評価した上で、最適なものを厳選します。製品そのものの評価だけではなく、素材評価を行うことによって、品質に万全を期しています。

機能提案からシステム検証まで自社完結する高度な電装開発
時代と共に高機能化していく自動車用シートの中には、多くの電装部品が搭載されています。その役割はさまざまで、安全や快適などシートの価値を高める重要部品となっています。当社では、お客さまへの新しいシートの機能提案から、その先の制御設定、システム検証までを自己完結で技術開発しています。

高度な試作検証技術による製品仕様の熟成
設計上は問題なくとも、実際に製品を造り上げる過程では、造り勝手の悪さや見映えの不具合が見つかることがあります。できあがった図面を基に、熟練した技術者が試作品を製作したり、CAE解析を行いながら、製品の精度や出来映え、量産にあたっての問題点などを検証します。
その問題点を各部門へフィードバックし改善を行うことで、製品仕様を熟成しています。
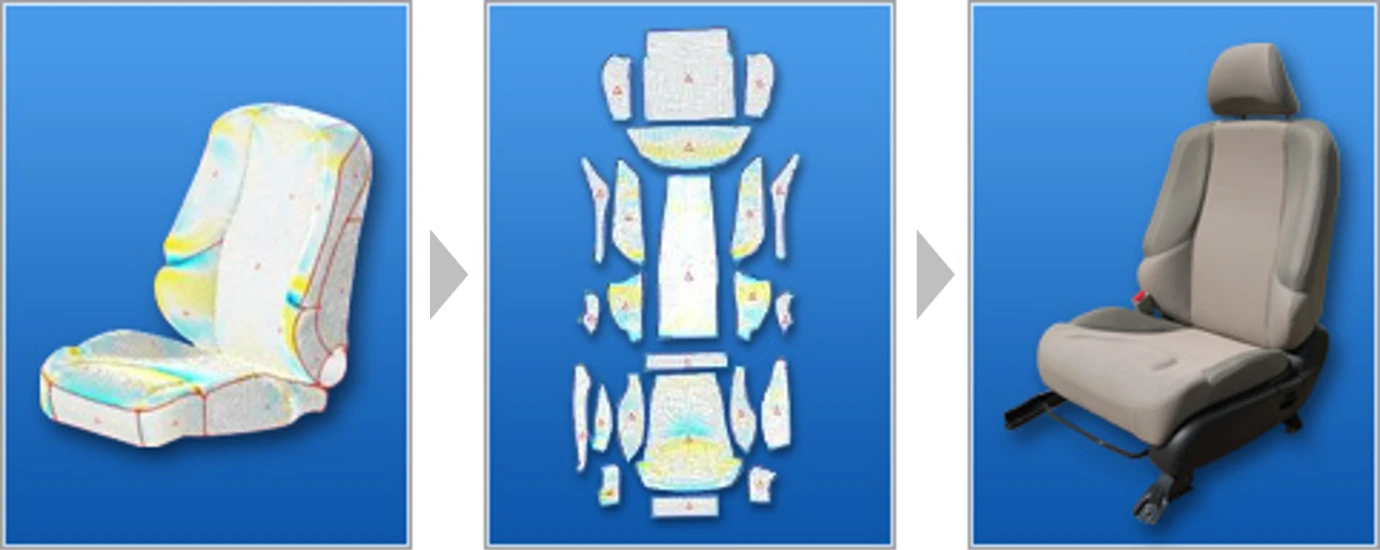
高精度の衝突試験によりシートの安全性能を実証
安全性能の高い製品の開発を実現するために、栃木県の「セイフティテクニカルセンター」および北米の「TS TECH AMERICAS, INC.」に合計3台のダイナミック試験機を設置しています。さまざまな観点から衝突安全性能のテストを行うことで、数多くの実験データを蓄積。高い精度の衝突試験及び評価が可能であるとともに、蓄積された実験データを活用した、CAE解析も行っています。
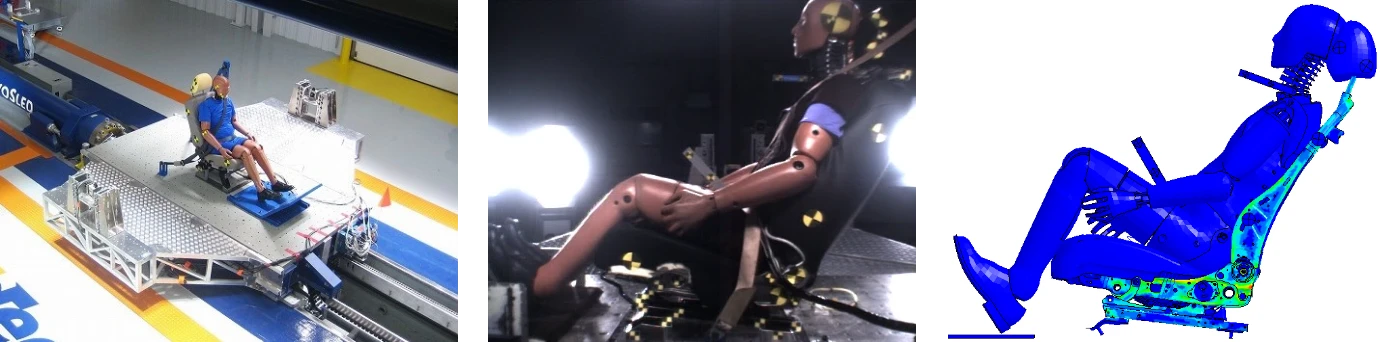